Hi everyone, Walter here, Senior Automotive Solutions Consultant at Fleet Alchemy. Today I’m delving into an innovation that has given classic car enthusiasts and automotive engineers around the globe a collective sigh of relief: 3D-printing parts for older vehicles. We’re talking about those niche, hard-to-find items such as brake line holders that can be as elusive as an unmodified Mitsubishi Evolution. Let’s embark on this fascinating journey where technology merges with vintage automotive restoration.
We’ve all been there – in the garage, under the hood of that beloved classic, only to realize that one little part you need to complete your restoration project is nowhere to be found. The maker hasn’t produced it in decades and your only hope is a scrap yard thousands of miles away… that may or may not have it. It’s a scenario many automotive enthusiasts are all too familiar with, and it used to be the breaking point for many restoration projects.
But now, enter the era of 3D printing, and suddenly, the unattainable becomes attainable, the impossible becomes possible. And it’s not just the obvious stuff like hood ornaments and badges; we’re talking about essential, intricate parts like brake line holders. It’s a fantastic application of this rapidly evolving technology that has the potential to revolutionize the entire automotive restoration industry.
Brake line holders might not be the most exciting part of a car but ask any automotive engineer and they’ll tell you they’re indispensable. These unsung heroes keep the brake lines in position, preventing them from vibrating or rubbing against other components and risking damage. Despite their importance, finding replacements for vintage or rare models can feel like searching for a needle in a haystack.
The process is innovative and relatively straightforward. Engineers begin by creating or obtaining a 3D model of the part – sometimes reverse-engineering the original if necessary – and then ‘print’ the piece using a variety of materials, such as plastics, resins, or even metals, depending on the 3D printer used. The result is a tailor-made, high-quality component ready for installation.
Moreover, the environmental implications of this approach are noteworthy. By producing only the parts we need, when we need them, we can drastically reduce waste and the carbon footprint associated with mass production and shipping. It’s a lean, mean, green approach to car restoration.
When you’re looking to test your next 3D print, need to develop a model, or want a hand in assembly and installation of these parts, reach out.
Until next time, stay driven.
Best, Walter
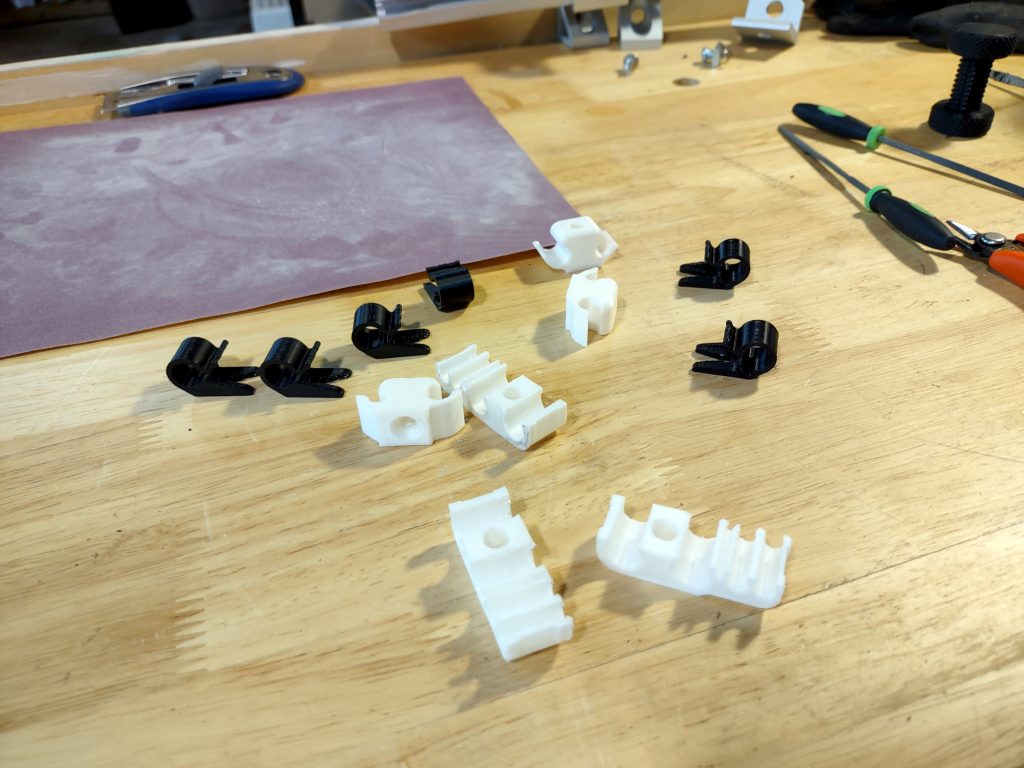
Leave a Reply