(HID) headlights once transformed how we see and navigate the night. But what happens when these high-performance systems malfunction or need a component replacement? A common issue that many people face is the replacement of an HID headlight ballast. This can turn tricky when the connectors are too large to remove from the housing, which is the case in a 2008 Toyota Prius and the focus of our discussion today. In our recent experience, we found that online guidance was adamant about cutting and splicing the wires. However, upon careful consideration, we decided that such a move could potentially lead to problems – based on the 2800 volts that this system operates on, any splices run a large chance of failure due to high voltage arcing. Instead, we embarked on an unorthodox, yet ultimately effective method of dismantling the connectors piece by piece, snaking them through the housing, and then reassembling them. Here, we share this experience and the valuable lessons learned along the way.
Step-by-step guide to replacing the HID Ballast:
The first step to addressing an issue is recognizing the problem. If your HID headlight is not turning on or is flickering, it’s a strong indicator that your ballast might be at fault.
To determine if the issue is a ballast of not, we swapped the headlight bulbs from left to right. Since the problem persisted on the same side, then the cause was likely a ballast.
Disconnect the Battery:
As a safety precaution, ensure the vehicle’s electrical system is inactive by disconnecting the battery before you begin.
Accessing the Headlight Assembly:
Remove the headlight assembly from the vehicle. The procedure varies by vehicle model, so refer to the user manual for specifics. In this case, this involved partial removal of the front bumper cover.
Identify the Ballast:
The ballast is a small box attached to the headlight housing. Locate this and disconnect the large connector.This is where the real challenge began. The connector was too large to remove from the housing, and the common guidance from online sources suggested cutting and splicing the wires.We approached the problem differently.
Dismantling the Connectors:
Rather than cutting the wires, we decided to dismantle the connector. This process required patience and precision. Using a small flat-head screwdriver, we carefully dismantled the plastic connector.
Navigating the Housing: After the connector was dismantled, each wire was then carefully snaked through the housing.
Ballast Replacement:
With the wires successfully navigated through the housing, we replaced the old ballast with the new one, ensuring the new ballast was properly secured in place.
Reassembling the Connectors:
After the wires were threaded through, they were carefully reconnected to the plastic connector piece by piece, in the original order. the replacement ballast had shorter wires so this necessitated a different path through the headlight housing.
Reconnecting the Assembly:
Lastly, we reinstalled the headlight assembly, making sure it was securely fastened and correctly aligned.
Testing:
Once the assembly was back in the car, we reconnected the battery and tested the headlights to confirm successful installation.
Lessons Learned:
What this experience emphasized was that outcomes are not always predictable, especially in real-time situations. Sometimes, what seems like the fastest and easiest solution could potentially cause more harm than good. In our case, while the method of cutting and splicing the wires could have been faster, it was likely to lead to more complex issues in the future. Thus, we opted for a more careful and thorough solution, which was to dismantle and reassemble the connectors. Although this route was more time-consuming, it avoided unnecessary risks and potential headaches down the line.One can apply this lesson to other areas in life and in business. There will be times when you encounter obstacles that seem insurmountable or confusing, and the most straightforward path could lead to unintended consequences. Instead of resorting to rash or easy fixes, consider alternatives, even if they require more time and effort. Additionally, this experience highlights the importance of problem-solving skills. We were faced with a situation that seemed to have only one solution – the prevalent advice was to cut and splice the wires. However, we chose to think outside the box, which led to a more favorable outcome. Thus, creativity and lateral thinking can prove to be invaluable when dealing with unique and complex problems – also it’s important to remember that the fastest way through is not always the best way – sometimes, going sideways is the way to success. Whether you’re an automobile enthusiast or a novice just starting to get your hands dirty, remember that every challenge brings an opportunity to learn grow.
Until next time, stay driven.
Walter
Senior Automotive Solutions Consultant,
Fleet Alchemy
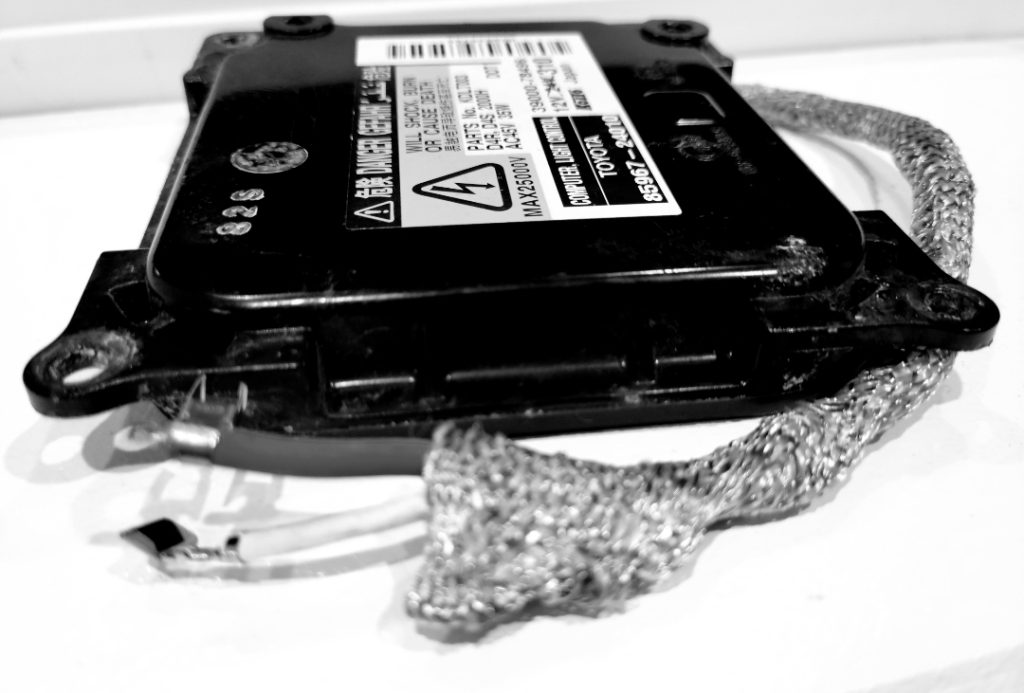
Leave a Reply